Professional Guidance on What is Porosity in Welding and How to Address It
Wiki Article
Porosity in Welding: Identifying Common Issues and Implementing Finest Practices for Prevention
Porosity in welding is a pervasive problem that commonly goes undetected until it triggers significant issues with the stability of welds. This typical problem can compromise the toughness and longevity of bonded structures, presenting safety and security dangers and resulting in costly rework. By recognizing the origin of porosity and applying efficient prevention techniques, welders can substantially enhance the top quality and reliability of their welds. In this discussion, we will explore the key aspects contributing to porosity development, analyze its damaging effects on weld performance, and discuss the very best techniques that can be taken on to lessen porosity occurrence in welding procedures.Common Root Causes Of Porosity

Making use of filthy or wet filler materials can present contaminations right into the weld, adding to porosity concerns. To minimize these usual causes of porosity, complete cleaning of base steels, appropriate shielding gas selection, and adherence to ideal welding criteria are essential techniques in accomplishing high-quality, porosity-free welds.
Influence of Porosity on Weld High Quality

The visibility of porosity in welding can dramatically endanger the structural integrity and mechanical homes of bonded joints. Porosity creates voids within the weld steel, deteriorating its general toughness and load-bearing ability.
Welds with high porosity levels tend to show reduced effect stamina and decreased ability to deform plastically before fracturing. Porosity can restrain the weld's capability to effectively transfer forces, leading to premature weld failure and possible security risks in vital frameworks.
Best Practices for Porosity Prevention
To enhance the structural stability and top quality of bonded joints, what certain measures can be applied to decrease the incident of porosity during the welding procedure? Using the proper welding strategy for the specific material being welded, such as changing the welding angle and gun setting, can better protect against porosity. Regular examination of welds and instant remediation of any kind of concerns determined throughout the welding procedure are crucial practices to avoid porosity and produce top quality welds.Significance of Appropriate Welding Strategies
Implementing appropriate welding strategies is extremely important in making certain the structural integrity and quality of welded joints, building on the foundation of effective porosity avoidance measures. Welding methods straight impact the total stamina and sturdiness of the bonded structure. One key aspect of correct welding strategies is preserving the appropriate heat input. Excessive warmth can bring about boosted porosity because of the entrapment of gases in the weld pool. Conversely, not enough warm may result in insufficient fusion, creating potential weak factors in the joint. In addition, utilizing the ideal welding parameters, such as voltage, current, and take a trip rate, is essential for accomplishing sound welds with very little porosity.Furthermore, the option of welding procedure, whether it be MIG, TIG, or stick welding, need to line up with the specific requirements of the job to make certain ideal outcomes. Correct cleansing and prep work of the base metal, as well as picking the best filler product, are additionally necessary parts of proficient welding strategies. By adhering to these best methods, welders can decrease the risk of porosity formation Get the facts and create top notch, structurally sound welds.
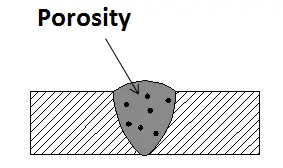
Evaluating and High Quality Control Procedures
Quality control actions play an essential function in validating the stability and integrity of welded joints. Checking procedures are necessary to spot and avoid porosity in welding, making sure the toughness and longevity of the final item. Non-destructive testing methods such as ultrasonic testing, radiographic screening, and aesthetic examination are commonly employed to recognize prospective flaws like porosity. These methods enable the evaluation of weld top quality without compromising the integrity of the joint. What is Porosity.Post-weld evaluations, on the other hand, analyze the last weld for any type of issues, consisting of porosity, and confirm that it meets specified requirements. Carrying out an extensive high quality control plan that consists click for more of complete testing treatments and assessments is paramount to lowering porosity issues and making certain the total top quality of welded joints.
Verdict
To conclude, porosity in welding can be an usual problem that impacts the top quality of welds. By identifying the typical sources of porosity and executing ideal methods for avoidance, such as correct welding methods these details and testing procedures, welders can ensure premium quality and dependable welds. It is vital to prioritize avoidance techniques to decrease the occurrence of porosity and keep the integrity of welded frameworks.Report this wiki page